Taking (material) responsibility: ZF Vigo in Spain takes compounding into its own hands with DCIM
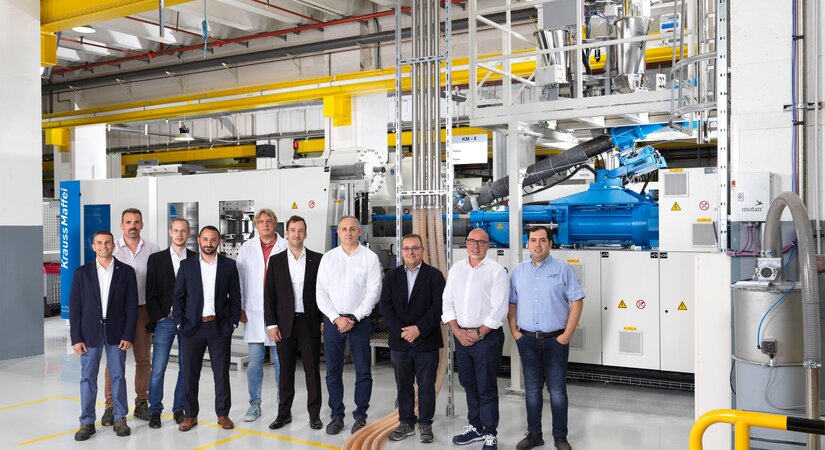
- DCIM (Direct Compounding Injection Molding): Developing, testing and protecting proprietary formulations
- Attractive cost-effectiveness for part weights from 50 to 2,000 grams with single-screw extruder
- KraussMaffei: 20 years of experience in direct compounding
(Munich, November 09, 2022). The mechanical requirements for a component change, new projects are assigned. The question of materials is ever-present. In response, ZF Vigo is able to develop and produce its own formulations—with the DCIM (Direct Compounding Injection Molding) process from KraussMaffei. It now makes the process attractive even for small and medium component weights.
The demands placed on plastics processors with regard to transparency and traceability are constantly increasing. When there is an issue with a part, it is crucial to find the precise cause. Is it due to the process; is it due to the material? At ZF Vigo in Spain, the company wanted to improve this process further to achieve the best possible transparency. The new DCIM process from KraussMaffei provided the answer.
Particularly cost-effective for small and mid-sized components
With its single-screw extruder, DCIM (Direct Compounding Injection Molding) offers the right equipment for small and mid-sized components. A profitability advantage is gained at shot weights from 50 to 2,000 grams. DCIM expands the proven IMC system (Injection Molding Compounder, with twin-screw extruder), and it is an addition to the portfolio. IMC is primarily suited for articles weighing 1,500 grams or more.
The DCIM single-screw extruder is installed in a space-saving piggyback position on a standard hydraulic injection molding machine (usually the GX series). Both operate intermittently. This means that the extruder stops automatically every time the injection volume for the next cycle has been reached.
Achim Härtel, Core Engineer Plastics at ZF, values the energy-efficient advantages of DCIM. The entire process is performed in one heat, since the compounded melt enters the plasticizing unit of the injection molding machine without any intermediate stop or cooling. This reduces polymer degradation, cuts energy costs and reduces the CO2 footprint.
The project team for successful direct compounding at ZF Vigo (from the left): Eduardo Casas (ZF, Injection Molding Specialist), Edgar Lopez (ZF, Manufacturing Engineer), Thomas Drogi (KraussMaffei, Process Engineer), Christian Seyferth (KraussMaffei, Global Expert Sales), Achim Härtel (ZF, Core Engineer Plastics), Jacob Seco (ZF, Manufacturing Engineer Specialist), Jose Trasobares (ZF, Manufacturing Engineering Manager), Angel Lemus (Coscollola, Director Post-Venta), Antonio Muñoz (Coscollola, Director Comercial Inyección), Ramazan Baser (Motan-Colortronic, Project Engineer)
Reliably processing of materials, including those with medium viscosity
DCIM technology from KraussMaffei can also be used to process materials with medium viscosity, whereas concepts from other providers only allow for embedding fibers in a low-viscosity matrix. The higher the viscosity, the better the mechanical properties of the components, which is important above all for safety-related products such as what ZF Vigo manufactures
The DCIM screw ensures perfect homogenization of the base polymer, added fibers, additives and masterbatch. It was specifically developed for this and has an unusually large ratio of length to diameter of 30 L/D (standard injection molding machines have a ratio of 17-23 L/D).
Maximum flexibility and get a fast ROI
Technical parts that come into question for direct compounding usually have cycle times of 20 seconds or more. In these cases, the additional material processing is done without affecting cycle time at all. If no compound is needed, the DCIM machine can also be used as a standard injection molding machine without any elaborate conversion work. As a result, the plastics processor obtains maximum flexibility—above all because the added expense for investing in DCIM pays for itself within a few months.
Recycled materials and bioplastics
DCIM will become of interest particularly with respect to processing recycled materials, bioplastics and natural fibers—this is what Jacob Luis Lopez, Manufacturing Engineer Specialist at ZF Vigo, believes. The competition in the automotive sector right now has gotten so fierce that you always have to be one step ahead.
Gaining control over the material used is a valuable option. That way it is easier for you to take over responsibility for the entire product as well as to gain a competitive advantage by creating, testing and protecting formulations yourself.
Contact Person
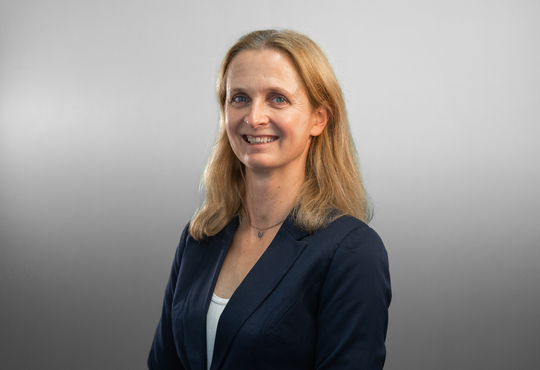
Marketing Manager Injection Molding Machinery & Contact Extrusion
Petra Rehmet
Tel +49 (0) 89 8899 2334
Mail to Petra Rehmet