More efficient spraying with KraussMaffei
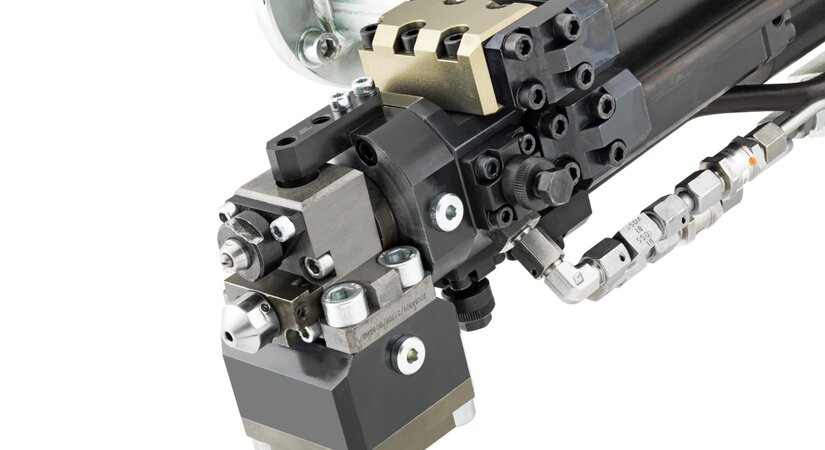
- Spraying PUR using the SCS process
- Flexibility by innovative nozzle change technology
- From flat to round jet nozzle in seconds
(Parsdorf, Germany, December 07, 2023) A wide bristle brush creates more surface area than a round brush, which is better suited for details. What everyone knows from painting also applies to spraying PUR using the SCS process. However, applications usually require both - and KraussMaffei offers the necessary flexibility with its innovative nozzle change technology. From flat to round jet nozzle in seconds - and the other way round.
SCS (Structural Component Spraying) is amazing: a paper honeycomb layer pressed with a glass fiber mat and visible fleece can withstand considerable weights as a loading floor in the trunk or on car roofs. The prerequisite for this is polyurethane (PUR), with which the glass fiber mat was previously sprayed. There are different areas here: the large surface itself and the edge zones, which need to be reinforced so that they are not damaged by the sharp tool edges that punch at the same time. Local reinforcement is also often necessary for metal or plastic inserts. So you need both a spray nozzle that covers large areas and one that places the PUR very precisely.
KraussMaffei was the first to succeed in establishing a process on the market in which both (each with its own mixing head) are operated on a robot and to patent a special device for this purpose. This was followed by a mixing head with a changeover device and finally a changeover module, with which it is possible to swivel from one nozzle to the other within a few seconds. Patent applications have been filed in various countries, some of which have already been granted. The team led by Alexander Berg and Ralf Moser developed the interchangeable piston, and Fredrick Su, as a sales representative, knows the customers who are already using it. Such as the automotive supplier Trèves. Sergi Salart (South Europe Industrialization Manager) emphasizes: "The efficiency of our spraying process in Treroc / Morocco is mainly based on the nozzle changing system. We are so satisfied that we will soon be introducing it at our plant in Romania too."
What are the advantages of the new technology? Compared to the conventional method of operating two robots with one nozzle each? It saves considerable investment costs. However, it is also common in the industry to use either the flat or round jet nozzle for the entire process - which also has disadvantages. A look at the discharge quantities and geometries is helpful here. A round jet nozzle has a throughput of around 50 grams / second and the maximum spray width is 120 millimeters. Atomization is carried out with air, the spray pattern is conical and the polyurethane track on the flat glass fibre mat is clearly rounded. The flat spray nozzle, on the other hand, delivers up to 130 grams / second and works without air support. The mat has a rectangular shape.
The flat jet nozzle is ideal for those who want to wet a large area in a short time. However, it will use more PUR than necessary, as superfluous areas are also covered when reinforcing the edges. The round jet nozzle, on the other hand, requires considerably more time, but it can precisely target the edge areas for reinforcement.
Switching between flat and round is therefore the ideal solution - but it has to be fast. The nozzle change module fulfills this requirement. For example, if you start with the flat jet nozzle and have completely sprayed the loading floor, the discharge channel is cleaned in around three seconds using compressed air. The change to the round nozzle itself is carried out hydraulically by pushing the second channel geometry into position. This only takes around 100 milliseconds and the process continues. The mixing head is equipped with spring-loaded nozzles or nozzles with vario equipment in order to be able to handle the variable material quantities. The latter work with an air cushion located in a gas chamber behind the nozzle. In the event of fluctuations in the component throughput, vario nozzles balance the pressure better and achieve optimum process parameters with different discharge rates.
pressing of the components and finally the PUR reaction time. How much can be saved when applying PUR can be calculated and depends on the respective application. For a component measuring 2200 x 1200 millimeters, the spraying time is reduced by up to 30 percent.
Anyone planning a new system for PUR processing would be well advised to invest in changeover technology right away, as Sergi Salart from Trèves emphasizes:
Contact Person
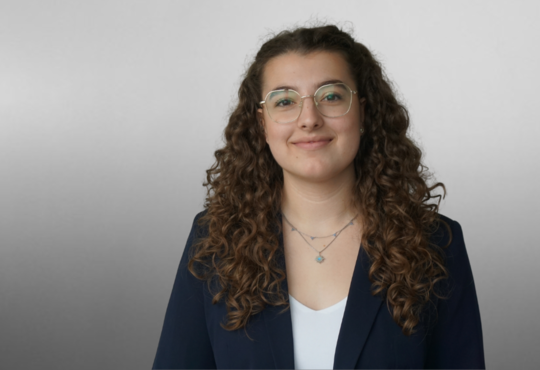