KraussMaffei supplies highly efficient extrusion technologies for ground-Breaking PureCycle recycling process
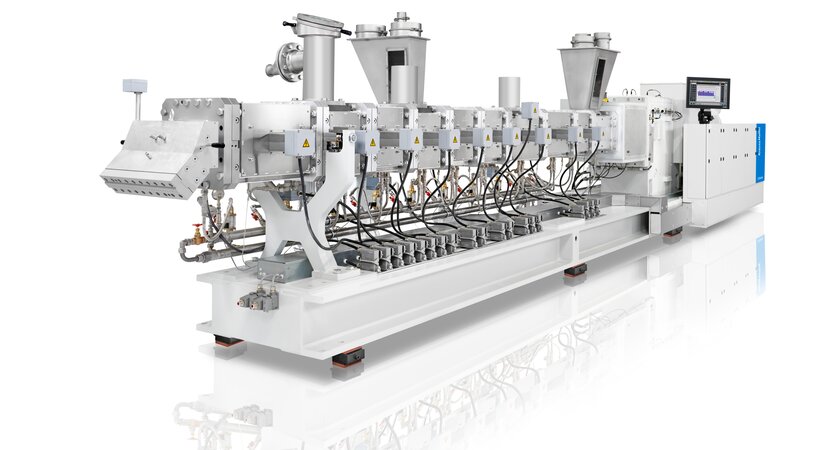
- PureCycle set new standards in plastics recycling
- Processing up to eight metric tons of PP waste carpet per hour
(Hannover, 8 September 2021) Stock market listed PureCycle Technologies (Nasdaq: PCT) launches a multi-million dollar recycling project in the USA.
PureCycle uses a highly innovative process to convert carpet scraps based on polypropylene (PP) composite material into high-purity pellets that are equivalent to virgin material. The company’s flagship plant is underway in Ohio and is scheduled to begin operating at scale in 2022. The plant will be equipped with several extruders delivered by Hannover-based KraussMaffei Extrusion, based primarily on its unparalleled expertise and uncompromising customer support.
“We are extremely pleased about this order and the trust PureCycle has placed in us,” says Carl Philip Pöpel, Director of Product Management at KraussMaffei. “Acting as a full-line provider of various extrusion technologies, we are in a position to deliver an outstanding high-performance package solution that enables efficient and resource-conserving plastics recycling and offers substantial added value.”
PureCycle sets new standard in plastics recycling
PureCycle uses proprietary technology licensed from The Procter & Gamble Company (P&G) to recycle waste PP into ultra-pure recycled-PP for applications spanning consumer goods, automotive, building and construction, and industrial uses.
“Thanks to PureCycle’s technology, we have succeeded in removing all impurities, odors, and dye residues from carpet remnants so that the PP pellets produced are equivalent to virgin material, both in terms of appearance and mechanical properties,” explains Brett Hafer, VP Manufacturing at PureCycle. “Now that PureCycle has passed the pilot phase successfully, we are building the world's most modern PP recycling line.”
Processing of up to eight metric tons of PP waste carpet per hour
The core component of the new PureCycle line is the extraction process. The technique cleans melted PP composite material from dye residues, foreign plastics and odors, providing for a pure PP melt and a recycled, re-usable co-product. The circulating solvent is then purified and returned to the process.
Two twin-screw extruders from KraussMaffei serve for melting the dry PP carpet scraps that are used as feedstock for the PureCycle process. These extruders are characterized by their ideal ratio between free volume and high specific torque, which makes them the first choice for processing the large-volume carpet scraps. Thanks to the high torque density of up to 16 Nm/cm³, they plasticize the starting material even at moderate temperatures and low speed and thus ensure optimum material homogenization and minimum energy consumption. Both high-performance extruders supply up to 8 metric tons of processed feedstock per hour via a melt pipe into the PureCycle process.
After passing PureCycle’s first processing stage, the cleaned melt is fed into the degassing extruder specifically designed to effectively remove any high-molecular residual monomers. Volatile matter like solvent residues and other impurities, such as adhering odorous substances and low-molecular compounds, are gently separated from the melt. The result is pure PP pellets that can easily be used to manufacture a wide variety of products by injection molding or extrusion coating processes.
“The collaboration and support we received from KraussMaffei has been exceptional. Collectively, we achieved real technical innovations and developed an exceptional solution for our process. We look forward to continuing this relationship as we scale our Ultra-Pure Polypropylene Technology globally,” said Scott Brown, Vice President of Program Management at PureCycle.
“We are exceedingly proud that – based on the tests carried out in our R&D center and the jointly developed modular concept – PureCycle has opted for KraussMaffei's extrusion technology and that we can now make a decisive contribution to the world's most modern PP recycling plant,” says Carl Philip Pöpel.
The complete installation of the plant will be an important milestone in the history of plastics recycling.