KraussMaffei at NPE: “Make plastic green” – Innovative solutions for circular economy and reducing the CO2-footprint
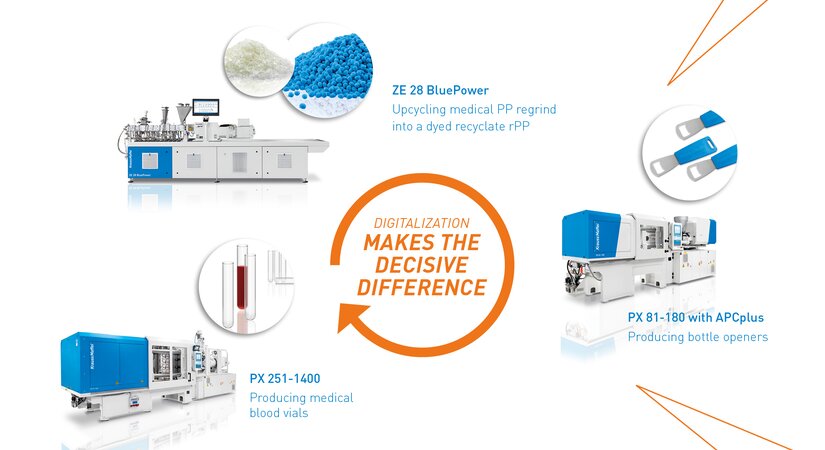
- Entire material cycle live @NPE: From medical blood vials to bottle opener
- Saving CO2 and costs with DCIM (Direct Compounding Injection Molding)
- New MuCell screw with 30 percent more plasticizing performance
- Live production of matrix lenses made of LSR
- Partnership with NIAR and Clemson University
- US market debut of additive manufacturing solutions
(Parsdorf, Germany, March 4th 2024) “Make plastic green – with high quality and efficiency” – this is KraussMaffei’s motto at the NPE show in Orlando, Florida (May 6 to 10, West Hall, booth W 600). Front and center of the trade show appearance are innovative technologies and solutions of injection molding, extrusion, reaction process machinery, automation and additive manufacturing focusing on circular economy and reducing the CO2 footprint.
"Sustainability is an added value - for us and for our customers. In line with our motto ‘We make plastic green’, we therefore aim to be a leading global supplier of sustainable solutions for the plastics processing industry”, explains Nolan Strall, President KraussMaffei Corporation. In order to achieve these goals, the circular economy is a supporting pillar of KraussMaffei's corporate strategy.
Circular Economy live @NPE
Trade show visitors at NPE can experience the entire material cycle, from a short-live medical blood vial to a long-live bottle opener, at the KraussMaffei booth. Starting with injection molding on a PX 251-1400, moving on to the upcycling process and to the twin-screw extruder ZE 28 BluePower and then to the all-electric injection molding machine PX 81-180, KraussMaffei demonstrates everything from valuable utilization of raw materials from disposable articles to production of premium quality components with a long service life.
The all-electric PX 251-1400 produces 32 medical blood vials per shot from PP 9074 MED material supplied by ExxonMobil. After shredding, these vials serve as base material for the up-cycling process carried out on the ZE 28 BluePower twin-screw extruder. Here, various additives such as bonding agents and liquid pigments are added, mixed and homogenized. The resulting re-compound is transferred to the downstream injection molding machine – more precisely to the an all-electric PX 81-180.
As recyclates can cause significant process fluctuations due to different viscosities, the PX 81-180 is equipped with APCplus. This machine function reliably compensates for these fluctuations. This allows components to be produced with consistently high quality with scrap reduced to a minimum - another important contribution to greater sustainability.
Saving CO2 and costs with DCIM
Another highlight form the area of sustainable solutions at the KraussMaffei booth is the DCIM process (Direct Compounding Injection Molding) with which up to 50 percent of material costs can be saved, also giving the processor considerably more freedom and control in the development of formulas. For DCIM, a single-screw extruder is installed in a space-saving piggyback position directly over the injection unit of a standard hydraulic machine.
The compounded melt is conveyed into the plasticizing unit in a single heating process, which reduces degradation of the polymer. In addition, the one-step process conserves energy and reduces the CO2 footprint. At the NPE show, a GX 1100-4300 DCIM will produce rugged reusable crates made of three different recycled materials.
The intuitive machine function smartOperation allows the startup and control of the injection molding machine as easy as using a coffee machine. This not only enables defect-free machine operation but also increases process stability and thus boosts efficiency in production. In particular, machine operators without in-depth prior knowledge of injection molding technology benefit from the advantages of smartOperation.
New MuCell screw with 30 percent higher plasticizing performance
MuCell can do everything that's currently in demand—generate savings on material, energy and investment costs—and thus noticeably reduce the CO2 footprint of products. At the NPE show KraussMaffei is highlighting its new universal screw for MuCell applications with 30 percent higher plasticizing performance.
The new HPS-Physical Foaming screw has a longer three-zone area, which can be universally used for all plastics (with and without fiber reinforcement) and has a plasticizing capacity that has increased by up to 30 percent. This allows for the selection of lesser screw diameters than before, which significantly reduces investment and operating costs for the plasticizing unit, or for the generation of a greater output using a screw of the same size as before.
PX 121-180 SilcoSet: Live production of matrix lenses made of LSR
Silicones, and particularly the new generations of LSR (liquid silicone rubber), continue to conquer new application areas thanks to their excellent physical property patterns, offering great opportunity for growth. At the same time, however, they burden the processor with challenges when it comes to precision and process consistency in the injection molding process. At the NPE show, a PX 121-180 SilcoSet produces matrix lenses for the headlight industry.
The machine function APCplus supports a sustainable production here by continuously analyzing the injection molding process and quickly and accurately compensating for material- and environment-related fluctuations in melt viscosity. This ensures a consistently high component quality and thus minimum scrap.
The two cavity LSR matrix mold comes from mold specialist ACH Solution providing best temperature balancing even with longer scheduled downtimes. The ACH Servoshot 2G stands for precise needle valve regulation. The linear robot LRX 150 from KraussMaffei with EOT from ACH Solution allows an inline production with inspections, weight check and separation.
Large-scale production also in aviation – Partnership with NIAR
Another highlight at the KraussMaffei booth is the manufacturing demonstrator Frankenstein from the National Institute for Aviation Research (NIAR) at Wichita State University. It showcases different examples how to introduce automotive-matured ultra-high-rate manufacturing technologies to aerospace – a joint research program NIAR and KraussMaffei are driving forward with together.
In addition, NIAR will show the inlet duct of a 10-meter-long unmanned system manufactured using a proprietary meltable tooling concept developed by Fiber Dynamics, Wichita, Kansas/USA. A further highlight is an aircraft window plug that is currently undergoing certification efforts for aircraft passenger-to-cargo conversion activities at NIAR.
These composites parts are manufactured using the FiberForm technology developed by KraussMaffei. The process combines the thermoforming of organic sheets and injection molding in a single process. The result is particularly lightweight fiber-reinforced plastic components with a high level of strength. Until now, they have mainly been used in the automotive industry. The cooperation between NIAR and KraussMaffei has now paved the way for FiberForm to be used in aerospace applications as well.
Future mobility - Clemson University shows driverless concept vehicle
Another partner at the KraussMaffei booth will be Clemson University. They will showcase its advanced materials and manufacturing expertise via multiple projects in mobility industries. Specially highlighted is an ultra-efficient driverless concept vehicle designed for the year 2035.
Clemson students and faculty worked with ExxonMobil Chemical and Honda North America to engineer, build, and validate the prototype with a special focus on sustainability, resulting in a design with 18% plastics and composites by weight – nearly double the 10% market average. Built with reclaimed, lightweight, and recyclable advanced materials, the project exemplifies the highly translational and rapid R&D engineering possible at Clemson.
Ultra lightweight: Premiere for first HP-RTM bike in the US
TIME Bicycles, in partnership with KraussMaffei, Fraunhofer USA and Clemson University is raising the bar of composite bicycle technology through a special development project to introduce HP-RTM (High Pressure Resin Transfer Molding) to the cycling industry.
At the NPE show, they are showcasing the first, USA produced HP-RTM bicycle to the world. Visitors to the show have the possibility to register for a giveaway from the first production. Retail value of the complete bicycle is 8,000 USD. TIME Bicycles was founded in France in 1987 and is the leading European manufacturer of carbon fiber bicycles, specializing in Resin Transfer Molding (RTM).
More transparency and efficiency with socialProduction
All injection molding machines at the booth are connected to socialProduction via the KraussMaffei smartCube. The socialProduction product family enables intuitive monitoring of the injection molding machines, the production process and the condition of the machine components.
productionMonitor, for example, guarantees a quick overview of the machinery and helps to efficiently monitor each connected machine with intelligent production key figures. With processSupport, the process is monitored autonomously using artificial intelligence. The early detection of deviations and proactive communication to the operator increase efficiency.
The liveCare condition monitoring solution offers continuous online monitoring of the condition of the machine components. This enables the implementation of condition-based maintenance strategies. EnergyControl ensures that energy consumption is optimized. The module provides a detailed insight into the total energy consumption of the injection molding machine and the individual machine components, including energy-related CO2 emissions.
US market debut of additive manufacturing solutions
KraussMaffei has achieved a significant milestone by successfully introducing its additive manufacturing solutions and services in the EMEA market. Starting in the second half of the year, these industrial AM systems will also be available for the US market. A key component of this offering is the innovative LSAM (Large Scale Additive Manufacturing) system, powerPrint alongside the precisionPrint stereolithography system.
At the NPE, KraussMaffei will showcase current case studies and solutions that illustrate the impressive capabilities of powerPrint. The powerPrint excels in processing large parts while leveraging the advantages of 3D printing. With the capability to produce fully or partially filled structures, achieve a build volume of up to 10 m³, and simplify the implementation of complex designs, powerPrint presents a compelling alternative to conventional production methods across various industries and applications.
Excellent partner network
Further partners at the KraussMaffei booth at the NPE show are the following companies: Audia Plastics, Basell Polyolefine, Big Spielwarenfabrik, Brabender, BUNTING-Newton, BYK-Chemie, ColorLite, ConAir, Dow, ECON, HEKUMA, , iNOEX, Kärntner Montanindustrie, KONGSKLIDE, motan, Open X, Prospect Group, Repi, S.C.S Societa Construzione Stampi, Sikora, STÄUBLI, technotrans, Trexel, vasantha group and Vision.
KraussMaffei at NPE
WEST HALL A, Booth W600
Contact Person
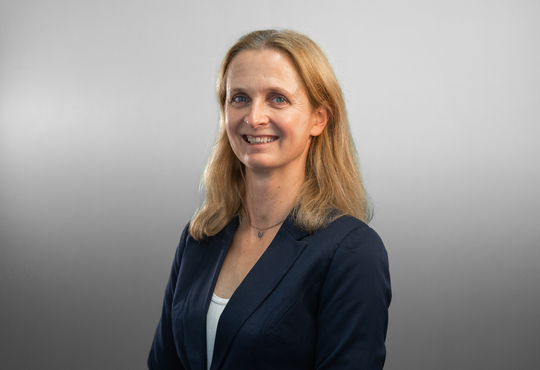
Marketing Manager Injection Molding Machinery & Contact Extrusion
Petra Rehmet
Tel +49 (0) 89 8899 2334
Mail to Petra Rehmet