From passenger to cargo aircraft: Renowned NIAR Institute relies on FiberForm technology from KraussMaffei
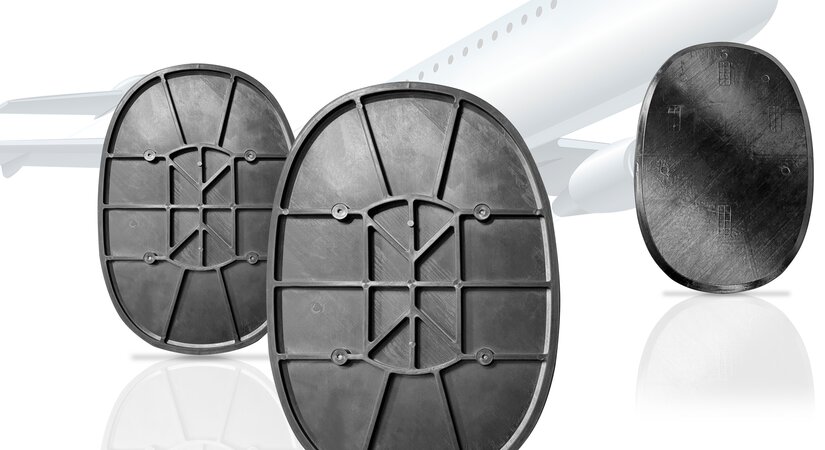
- Window plugs made of thermoplastics composites
- Significant weight reduction compared to metal solution
- Short cycle time: 40 parts per hour
- Joint NPE appearance
(Parsdorf, April 24, 2024). When two specialists cooperate, the conversion of passenger aircrafts into cargo planes can be made much more efficient. The National Institute for Aviation Research (NIAR) at Wichita State University in the United States, is renowned for investigating how modern composite technologies can be safely and efficiently used in aviation. KraussMaffei adds its high-rate production expertise gained from supporting the needs of the efficiency-driven automotive industry. The result is a successful example for metal replacement – and can be seen at the KraussMaffei NPE Booth in Orlando, FL (May, 6-10, 2024, booth W600).
There is even a separate word for this: preighter. Created during the coronavirus crisis, when hardly any people were traveling, it refers to a passenger jet used (temporarily) as a cargo plane. And the permanent solution is also common: aged airships that no longer offer the latest comforts still cut a good figure as cargo aircraft. Demand is high, as the purchase price is only a fraction of that of new aircraft.
Thermoplastic lightweight with FiberForm saves valuable cycle time
Amongst many other tasks, passenger to cargo conversions require replacing acrylic window plugs with metallic alternatives for ease of maintenance. This costly and time-consuming metallic solution can be further optimized by modern fiber-reinforced thermoplastic composites that offer the same stability at lower costs, less weight, and in a fraction of the time it would take to machine the metallic part. NIAR and KraussMaffei have been combining their expertise for the development of a lightweight solution using the FiberForm technology. With FiberForm, a fully consolidated fiber-reinforced thermoplastic sheet known as organosheet is inserted into the tool, formed and overmolded with a thermoplastic polymer.
In the case of the window plugs, this is done on a GXW 450-2000/1400 with a swivel platen. The window plug was designed with the oval-shaped geometry of the original with appropriate design modifications, ex., adding ribs to stiffen it to withstand pressure loads. In order to achieve the desired mechanical properties, the team of Dr. Waruna Seneviratne (NIAR) and Eugen Schubert (KraussMaffei) used high-performance plastics LM-PAEK reinforced with AS4 carbon fibers for the 16-ply organosheet and 30% chopped-fiber-filled PEEK for overmolding the ribs.
20 percent lighter than its metal counterpart
The short cycle time is one of the major advantages of fast injection molding compared to metal machining: 40 window closures can be produced within an hour. In addition, the thermoplastics used for FiberForm offer the possibility of welding components, have a high impact strength, are resistant to high temperatures, chemical and environmental influences and are also flame-retardant.
Compared to its metal counterpart (590 grams), the composite overmolded version of the window plug weighs 20 percent less. The team is already working on further optimizing the structure to make it about 40 percent lighter than the metallic counterpart. The next step for the NIAR program is to subject the window plugs to further functional tests required for certification – for example with regard to durability – so that it is ready for series production.
Successful transfer from automotive to aviation
The NIAR’s Advanced Technologies Lab for Aerospace Systems (ATLAS) is investigating issues such as these, and at the same time, training the specialists of tomorrow. A total of around 1,600 employees are active at six NIAR locations, with the total annual volume of R&D projects amounting to more than 300 million dollars.
Pushing together the introduction of thermoplastic lightweight construction in aviation:
Nolan Strall (President Krauss-Maffei Corporation), Dr Waruna Seneviratne (Director of NIAR ATLAS) and Eugen Schubert (Sales and Application Manager Krauss-Maffei Corporation) (from left to right)
Photo: KraussMaffei
NIAR and KraussMaffei have been partnering successfully for two years, and Dr. Waruna Seneviratne (Director NIAR ATLAS) points out: ”KraussMaffei “has not only set up a machine with multiple capabilities, but has also been actively helping us on-site with process development. Our students also gain a tremendous amount of hands-on experience and get to interact with the supply chain for several new capabilities we introduced in recent years. Our goal is to transfer the efficient processes such as FiberForm from automotive production to aviation.”
First place in SAMPE Technical Paper Awards
Dr. Waruna Seneviratne and Eugen Schubert have recently published a technical paper about this project. The paper with the title “Ultra-High-Rate Manufacturing of Thermoplastic Window Plug Using Hybrid Overmolding” has achieved 1st Place in the outstanding technical paper awards for SAMPE 2024. The winners will be acknowledged and honored at the SAMPE Awards Breakfast scheduled for May 23rd 2024.
Contact Person
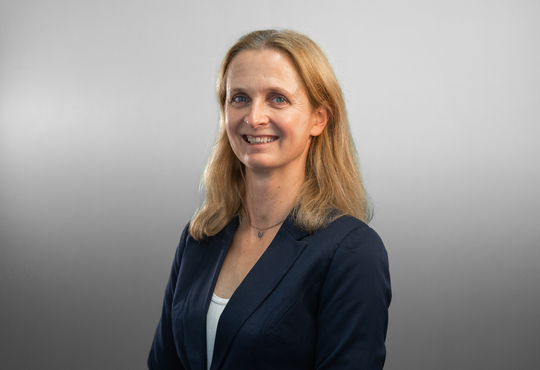
Marketing Manager Injection Molding Machinery & Contact Extrusion
Petra Rehmet
Tel +49 (0) 89 8899 2334
Mail to Petra Rehmet