Do it yourself – AsMoPLAST is getting into LSR processing with KraussMaffei—and building the mold on its own
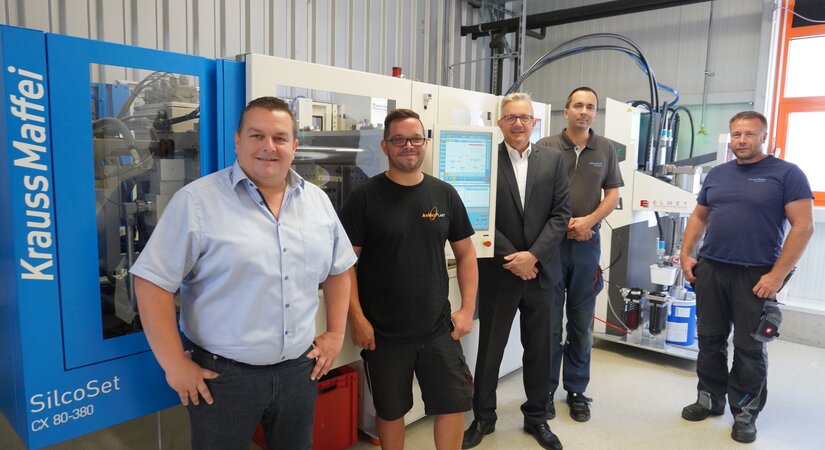
- First CX 80-380 SilcoSet in operation
- Crucial for investment: Support provided by the application technology from KraussMaffei
- Initial order from the area of personal care
Simon Zügel is interested in niche areas. As early as the beginning of the 2000s, the CEO of AsMoPLAST purchased molds from China before becoming an expert in global moldmaking and injection molding. Now he is exploring new terrain again with KraussMaffei. At the beginning of the year, AsMoPLAST decided to get into processing LSR (Liquid Silicone Rubber)—and built the mold for this on its own.
The first CX 80-380 SilcoSet was recently installed in a separate area of the production hall in Endingen and has already proven that Simon Zügel's plan is working. The silicone injection mold created in the company's own moldmaking department works perfectly and, starting next year, will be producing sophisticated hygiene products for women.
The CEO made a very deliberate decision not to commission one of the well-known silicone moldmakers, but instead to venture doing it alone. Since the material is extremely low-viscosity, the mold must be very well sealed. There is often a vacuum created to prevent leaks as well. The temperature control in the process is exactly the reverse as for thermoplastic. In other words, the melt must be cooled in the plasticizing unit to prevent premature curing and the mold, by contrast, is heated.
Successful start in silicone processing with an experienced partner
Due to these specific conditions, even experienced injection molders often shy away from getting into LSR technology, despite the fact that the silicone market has consistently high growth rates. AsMoPLAST is demonstrating that it works if you just dive in head-first. The silicone processing location has to be separate from the rest of production to prevent contamination. In Endingen they simply created a drywall partition for this purpose. Then you need an experienced partner for the machine technology. AsMoPLAST brought aboard the provider it has been confidently collaborating with for years. Five KraussMaffei machines of the CX and GX series with clamping forces from 500 to 6500 kN are already producing articles made of thermoplastic in Endingen near the Kaiserstuhl volcano.
Every part is a good part with the APC plus machine function
The intensive advising and support from the Application Technology department proved to be a critical criterion for actually placing the order with KraussMaffei. The APC plus machine function, which controls the filling quantity in the cavity from shot to shot and takes into account the melt viscosity as well as stored material parameters for this purpose, ensured that the machine produced good parts right from the first shot when it was commissioned. Silicones are generally subject to greater batch fluctuations than thermoplastics, which can result in overfilling or underfilling the component weight. In this respect, the use of APC plus here pays for itself exceptionally.
The current project uses only part of the capacity of the newly delivered LSR machine, so AsMoPLAST CEO Simon Zügel is already looking forward to offering the new technology to his existing customers before expanding to other areas. At the location in Endingen, an additional production hall is currently being built, which will be moved into in early 2022. Maybe then even more SilcoSets will follow.
Contact Person
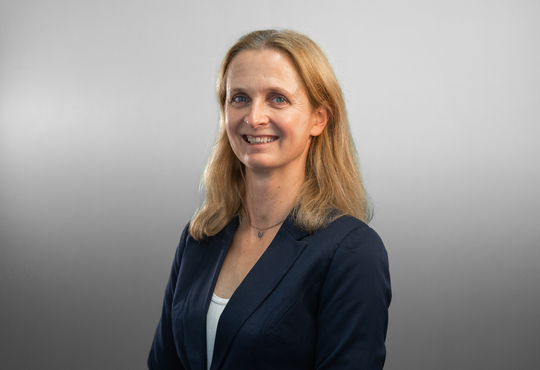
Marketing Manager Injection Molding Machinery & Contact Extrusion
Petra Rehmet
Tel +49 (0) 89 8899 2334
Mail to Petra Rehmet