Debut at K’ 2022: Energy monitoring for plastics parts
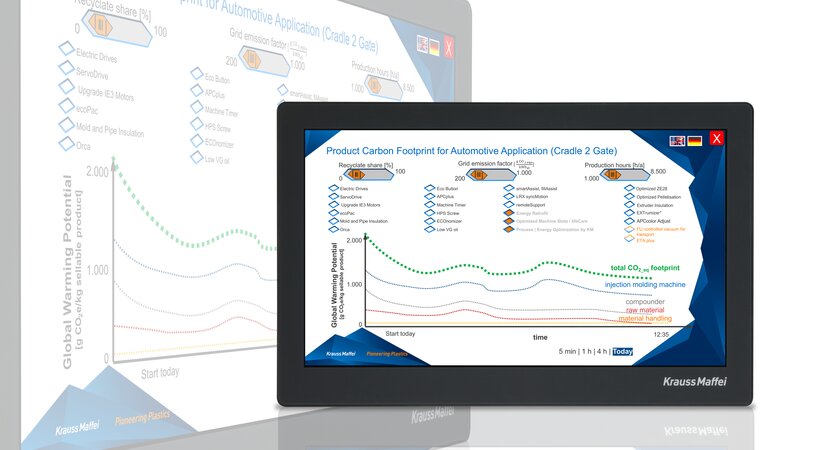
- KraussMaffei and Motan developed an application for optimizing the carbon footprint
- Live presentation for trade visitors: various levers for carbon footprint reduction
(Munich, 19 October 2022) What is the carbon footprint of the product you hold in your hands – taking into account the material input and, perhaps several production steps? And what is the difference when the part is made from recycled material? At K 2022 (hall 15, booth C 15 /C 24-D 24), visitors to the trade show will be able to see for themselves the new monitoring system developed by KraussMaffei and Motan that continuously visualizes the carbon footprint and allows it to be influenced by various levers.
Circular Economy is the guiding theme of KraussMaffei's trade show appearance at this year’s K. In keeping with this motto, the live demonstration of a closed material cycle illustrates how valuable raw materials can be saved using disposable items from the healthcare sector, for instance. Insulin pen caps, for example, are used only briefly by the millions and are then available as raw material for more durable applications. At the exhibition booth, these caps are produced from medical PP on a PX 200 MED injection molding machine, subsequently shredded and then fed into a ZE 28 BluePower twin-screw extruder, where up to 30% of glass fibers, coupling agents and liquid dye are added. The recompound obtained in this manner is led into the downstream powerMolding 1300 injection molding machine to produce a front end carrier for the automotive industry.
What is the impact of a 30, 50 or 100 percent proportion of recycled material on the carbon footprint of this front end carrier? And what is the point of operating the injection molding machine with APCplus – an innovative digital product that ensures a more stable weight consistency of the parts and thus avoids scrap? Does the origin of the electricity consumed really affect the CO2 balance as much as is generally assumed?
At two points in the Circular Economy exhibit area, interested visitors can get answers to precisely these questions in a playful manner.
Nevertheless, the background is definitely real: Customers are increasingly asking plastics processors about the carbon footprint their product actually generates. In addition, stricter EU regulatory requirements will have to be complied with in the future. KraussMaffei and Motan demonstrate potential solutions with a jointly developed application that incorporates live machine power consumption data on the one hand and material flows on the other in calculating carbon footprints. The curves shown reflect what really happens on a trade fair day: high CO2 emissions in the morning when the still cold machines are started and the subsequent drop in CO2 emissions when the extruder and the injection molding machine have reached their operating temperature.
Trade visitors can use sliders to change the reclaim share in the input material, the emission factor of the power consumption based on renewable energy generation or coal-fired power generation and the annual production hours. By means of buttons, special features such as the energy-optimized BluePower drive, thermal insulation of the plasticizing section or extruder, or the Eco-button can be switched on or off during calculation.