Coating in the mold with ColorForm - in a new dimension
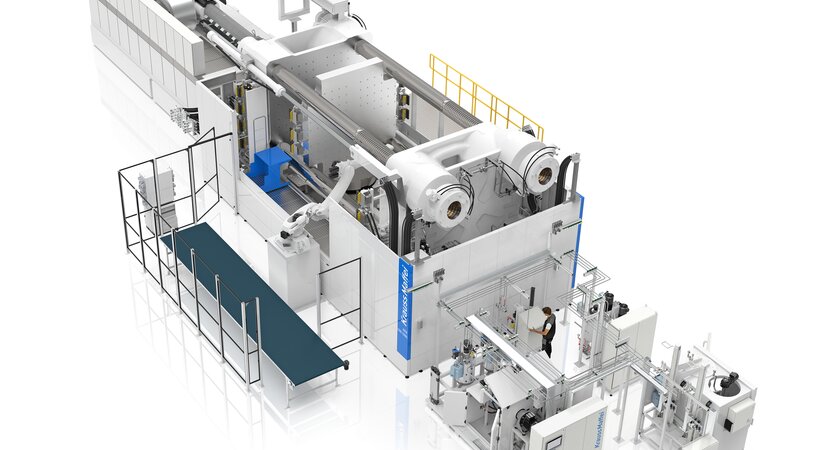
- KraussMaffei puts the largest lab system for polyurethane flooding into operation
- MXW injection molding machine with 45,000 kN, 2 RimStar metering systems, 3 different mixing heads
- Polyurethane material discharge: up to 500 g/s
- Complete project scope from a single source: injection molding, reaction process machinery, automation, post-processing
(Parsdorf/ Germany, July 31, 2024) Environmental regulations for paint shops are becoming increasingly strict – not only in Europe, but also in China, for example. In addition, downstream processes are consuming more and more resources for logistics and subsequent handling. With KraussMaffei's ColorForm process, coloring is done directly in the injection mold by coating thermoplastic components with a polyurethane or polyurea layer (PUR/PUA). KraussMaffei's Parsdorf site is now home to the industry's largest new lab system, e.g. for the production of outer skin components for vehicles.
Just make the machine bigger: When it comes to complex technical processes, it's not quite that simple. Careful planning was also required for the new ColorForm lab system. The aim was to map the complete production process for customers in an "all in one" process (injection molding, PUR flooding, parts handling, post-processing and surface treatment) and to be flexible for medium and (very) large components. The possible production of sample plates was also taken into account. The result is an MXW 4500 with swivel plate and widened clamping plates plus several so-called wet parts that provide the polyurethane. A RimStar Flex 8/8 metering system with MK5 / MK8 mixing heads handles quantities of up to 50 g/s and 250 g/s respectively. Another available system is the RimStar Compact 16/29 with the newly developed MK10-3K mixing head, which achieves output rates of up to 500 g/s
Depending on the component weight, the paint is added via a modular dye module (with the 2K mixing pots) or added directly, such as with the MK10-3K. This had to be taken into account in the complex routing of media supply lines in the entire system.
The automation was also designed with practicality in mind. As some plastics (such as PP, PA, PE) need to be activated to ensure adhesion between the thermoplastic and polyurethane, a flame treatment station is integrated into the lab system. The system is expanded through the addition of a trimming cell, which can then be used to remove the sprues from the components. This technology also comes from KraussMaffei.
Two unique products from the digital portfolio, which have been put on the market, round off the overall offering: The APCplus machine function on the MX4500 serves as an autopilot for the injection molding process and guarantees extremely weight-constant components by adapting the changeover point and holding pressure to the melt viscosity from shot to shot. In addition, the dataXplorer monitors the entire process and records more than 1000 machine signals in curve form with a resolution of up to 200 Hz. This gives the user a microscopically precise view of all subprocesses of the ColorForm process and complete traceability.
KraussMaffei is the only supplier in the industry to develop and manufacture all the components required for the ColorForm system - injection molding machine, reaction process machinery, automation, post-processing and digital products - in house. They are therefore perfectly coordinated and there are no interface problems. This is a decisive advantage, especially for customers who are new to PUR technology.
Contact Person
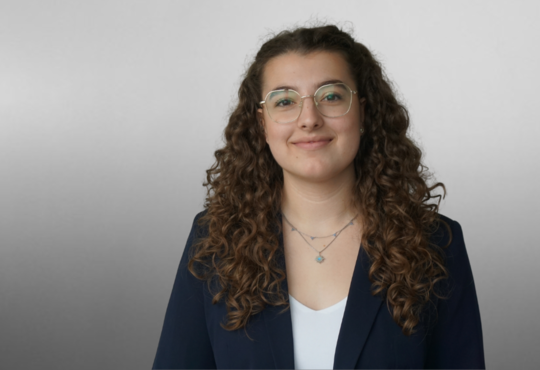