Capacity increase: nine at once
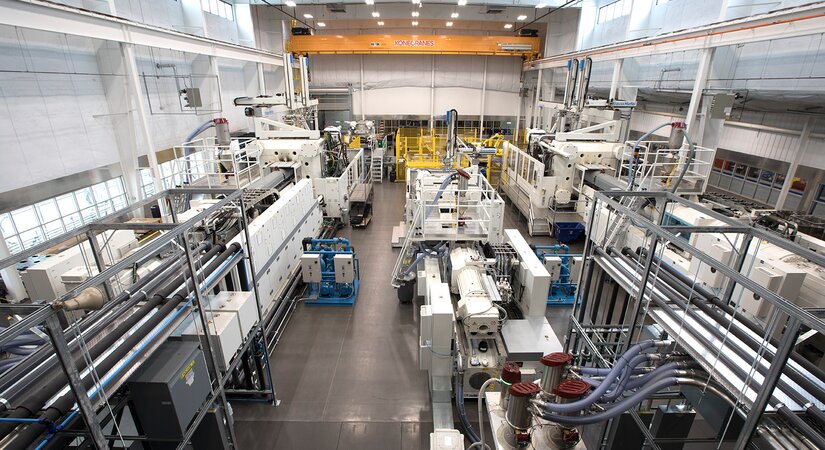
(Munich, September 6th, 2021) The building where they will be housed is not quite completed, but the new arrivals are already being eagerly awaited in Winchester, Virginia. They include two injection molding machines from the MX series (one MX 1600 and one MX 2300) and seven from the GX 1100 series, which Monoflo – a family-owned company – has ordered from KraussMaffei. The machines will produce reusable transport packaging at this location.
It is a highly competitive market with products that are standardized to a high degree and therefore comparable. For this reason, high value is placed on efficiency in production through fast cycle times and a high degree of automation. Monoflo specializes in articles such as pallets, pallet boxes and transport totes with and without lids and successfully supplies them to globally recognized companies such as Amazon, General Motors, Mercedes, and Aldi. The customers are predominantly from the logistics industry, followed by the automotive sector, automation sector, and the food industry.
"The coolest thing in the world" - Mold change within 9 minutes
Since 2015 KraussMaffei has been the machinery partner for systems with advanced technology. Currently 10 injection moldings machines of the MX series with clamping forces from 10,000 to 32,000 kN are operating 24/7. Two of them feature a highlight: an automatic quick mold change system that Monoflo CEO Henning Rader thinks is "the coolest thing in the world". As automotive customers of Monoflo sometimes need only 500 or 1000 units of a particular box, these molds must be changed relatively frequently. The net time for a mold change was previously 45 minutes, but it often took several hours of downtime before a skilled mold setter was available – especially during night shift. Now everything is automated, and – amazingly enough – only nine minutes pass between the last part from the old mold and the first part from the new mold. Henning Rader is a fan of the solution, saying that "two machines do the work of three.”
Other special applications from KraussMaffei are also at work in Winchester. In an MX 3200 TwinForm, two components of a collapsible bulk box are created in one shot. The components are bonded to each other afterward and since the charged material is often abrasive and sometimes highly viscous, the screws are designed and coated accordingly.
Focus on In-Mold-Labeling and recycled material
Monoflo pursues a highly proactive strategy in building up capacity and technologies. Thus, the company wants to use the new injection molding machines of the GX series to further establish the in-mold labeling technology in the US, where transport crates are usually still labeled with adhesive barcode labels even though an IML barcode application would be significantly more durable.
As Monoflo operates recycling plants on its own and blends 50 to 100 percent of regrind into its articles, the APC plus machine function is used with high intensity. Based on the melt viscosity and stored material parameters, the function re-regulates the shot weight for each cycle. While the industry assumes an average scrap rate of two percent, Monoflo consistently stays below one percent – and thanks to the precise part weight, the company also saves material that would be wasted by overpacking the part. Due to the current high material prices and the high production volumes, this definitely has an effect.
The collaboration between Monoflo and KraussMaffei began with a five-million-dollar investment on 2015 when Monoflo needed new machines for a new application. Ever since, the two companies have been developing in tandem, and Monoflo expects that the market will consistently grow over the next five years. Thus, further heavy machinery will surely make its way to Winchester in the future.
Contact Person
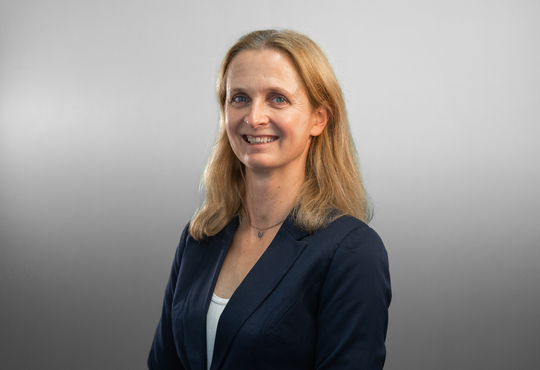
Marketing Manager Injection Molding Machinery & Contact Extrusion
Petra Rehmet
Tel +49 (0) 89 8899 2334
Mail to Petra Rehmet