3D-printed and mirror-smooth: KraussMaffei offers additive manufacturing and surface finishing from a single source
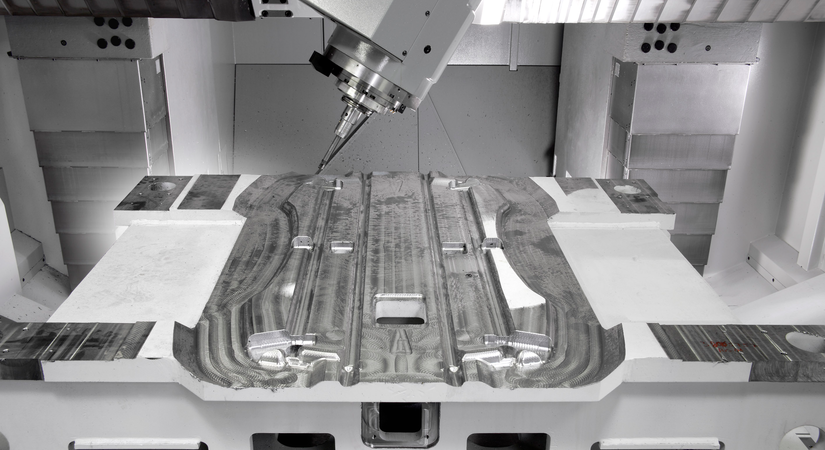
(Parsdorf, Germany, December 13, 2023) One-offs in industrial production quality - the best way to achieve this is with 3D printing. In order to straighten the strand structure created in this process, objects are post-processed, for example by milling. At KraussMaffei, the sites in Parsdorf (Additive Manufacturing) and Harderberg/Georgsmarienhütte (toolmaking) work together for this purpose. The customer receives his complete component from a single source.
- Unique items using 3D printing
- Seamless combination of additive manufacturing and surface finishing
- From large-format components to mirror-smooth surfaces
The powerPrint large-format printer can be used to produce components with dimensions of up to 2 x 2.5 x 2 meters - either by purchasing such a printer or by using print on demand. With this service, KraussMaffei takes care of the entire project, from data optimization to the perfect surface.
When customers first asked Ender Murat Ferat (Project Engineer Additive Manufacturing) in Parsdorf about this service, he did not immediately have his toolmaking colleagues in Harderberg in mind. No wonder, as they mainly work for the company's reaction technology division and produce molds for PUR processing, among other things.
Once contact had been established between the sites, joint development began. In Harderberg, they had already been milling plastic as well as metal, but mostly material made from Ureol, a polyurethane or epoxy resin saturated with fillers in sheet and block form. Production Manager Stefan Springrose explains: "Our products include prototypes and leatherette models for the automotive industry." Recycled PETG with 30 percent glass fiber reinforcement will now be used for 3D printing.
Milling plastics requires different machines to those used for metal, as the cutting process is simpler and involves more stock removal. For this reason, less powerful but highly dynamic machines are used to achieve the highest possible cutting speeds and fast production times. The tools used must be extremely sharp and require optimum chip removal. During tests with the glass fiber-reinforced PET, Thorsten Richter, team leader of the milling shop in Harderberg, even discovered "that diamond-coated milling cutters are necessary to withstand the abrasive material. This significantly reduces wear."
The edge structure familiar from additive manufacturing can thus be completely smoothed. To let customers feel how fine the surfaces can become, Ender Murat Ferat always has corresponding sample plates with him. So far, they have reached a roughness depth of RZ 12, but Thorsten Richter emphasizes that it is possible to get even smoother: "It just takes longer."
One project that colleagues in Bavaria and Lower Saxony have already implemented together is a sand casting mold for pressure pads. For this process, a negative mold is first produced, with which the actual sand mold is manufactured, which in turn holds the liquid metal (iron, aluminum, etc.). The sand mold is destroyed during demolding, and the milled 3D body can be used again and again. Until now, ureol was usually used for this. Despite the higher costs per kilo of raw material, additive manufacturing offers two decisive advantages: Firstly, the models are significantly more resistant to breakage, and secondly, you are independent of the standard dimensions of the ureol blocks and plates. These usually do not correspond to the dimensions required for the project, so they have to be glued together by hand to the required size. The associated labor costs can be saved if the 3D printer produces a blank that only needs to be built up where the end product requires material. This ultimately makes the 3D mold cheaper than its Ureol counterpart, despite the higher base price for the PETG.
The cooperation between additive manufacturing and toolmaking benefits both sides because each area can now offer additional services. Print on demand customers receive their workpieces from a single source with a perfect finish, while existing customers of Ureol models can use the more break-resistant PET GF30.
KraussMaffei is the only company in the industry that manufactures machines for all types of plastics processing - additive manufacturing, reaction process machinery, extrusion and injection molding. Technical developments are driven forward in the know-how network.
Contact Person
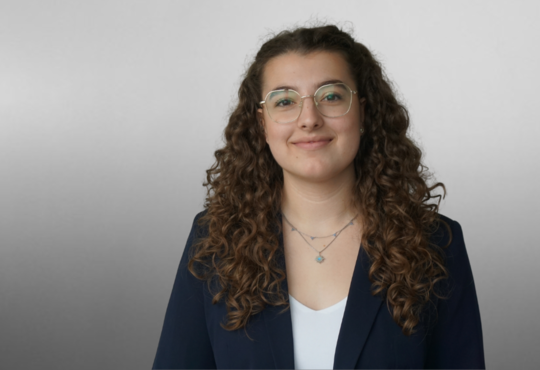