Rezeptur in eigener Hand: Fiber Dynamics investiert in GX 1100 DCIM von KraussMaffei
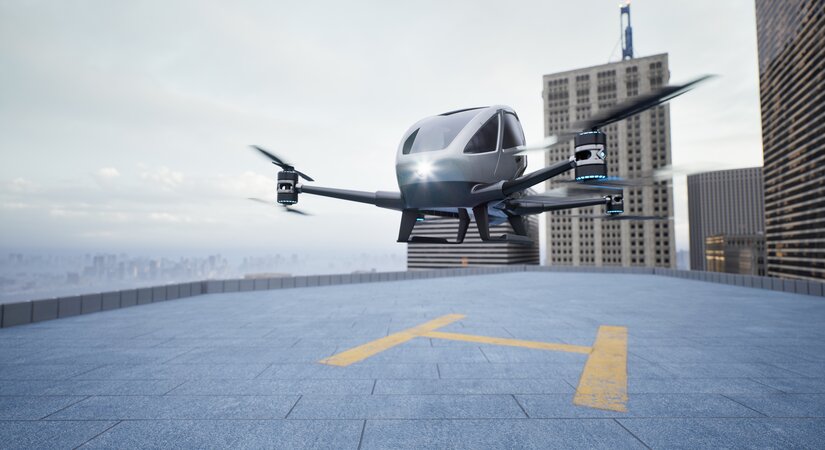
- DCIM (Direct Compounding Injection Molding): eigene Rezepturen kreieren, prüfen und schützen
- Bis zu achtmal schnellere Zykluszeiten im Vergleich zum bisherigen LCTS-Verfahren
- Weniger Energieverbrauch und besserer CO2-Footprint
(Parsdorf, 03.04.2024). Fiber Dynamics Inc. in Wichita im US-Bundesstaat Kansas ist ein Spezialist auf dem Gebiet hoch anspruchsvoller Composites-Lösungen. Mit der Investition in eine GX 1100-4300 DCIM von KraussMaffei steigt das Unternehmen in das thermoplastische Spritzgießen und zugleich in das Direktcompoundieren ein. Vorteile sieht Fiber Dynamics vor allem in der eigenen Rezepturhoheit und damit einhergehenden Flexibilität sowie in schnelleren Zykluszeiten und der hohen Wirtschaftlichkeit.
Mit seinen 100 Mitarbeitern entwickelt und fertigt Fiber Dynamics seit 40 Jahren hoch komplexe Artikel aus Verbundwerkstoffen. Die Kunden kommen aus den unterschiedlichsten Branchen, zum Beispiel aus der Luft- und Raumfahrt-, der Verteidigungs- oder Automobilindustrie. Im Fokus bei der Auslegung der passenden Lösung stehen neben bauteilspezifischen Eigenschaften, wie Gewichtsreduktion oder eine höhere Festigkeit durch integrierte Strukturen, auch zunehmend wirtschaftliche Argumente. Dazu zählen zum Beispiel die Eliminierung von sekundären Montageprozessen, ein höherer Automatisierungsgrad oder kürzere Zykluszeiten. Vor diesem Hintergrund ist Fiber Dynamics stets offen für neue wirtschaftliche Herstellprozesse.
DCIM deutlich schneller als bisherige LCTS-Lösung
Die Entscheidung für die DCIM-Technologie (Direct Compounding Injection Molding) fiel kurz nach der ersten Kontaktaufnahme mit KraussMaffei nach weniger als sechs Monaten. Zu dieser Zeit musste Fiber Dynamics die Produktion ausweiten und stand mit der Herstellung von Propellerblättern für den Advanced Air Mobility-Markt vor einer besonderen Herausforderung.
Die bestehende Lost Core Tooling System-Lösung (LCTS-Lösung) dauerte zu lange, wies Formulierungsbeschränkungen auf und war mit herkömmlichen Methoden zu kostspielig. Das Spritzgießen war eine offensichtliche Lösung, aber die Herstellung der proprietären und hochgradig kundenspezifischen Rezepturen stellte eine zusätzliche Herausforderung dar. „KraussMaffei war in der Lage, unser Problem schnell zu verstehen und uns mit seiner DCIM-Technologie eine einzigartige Lösung anzubieten. Darüber hinaus konnte KraussMaffei die Lösung eindrucksvoll vorführen und umsetzen“, lobt Darrin Teeter, CEO von Fiber Dynamics, die Zusammenarbeit.
Rezeptur in eigener Hand bringt klare Vorteile
Neben den bis zu achtmal schnelleren Zykluszeiten im Vergleich zur bisherigen LCTS-Technologie sieht Fiber Dynamics in der DCIM-Technologie vor allem den Vorteil in der eigenen Rezepturhoheit. „Die Fähigkeit, eine Vielzahl verschiedener Rezepturen zu testen und schnell neue zu entwickeln, ist entscheidend für den Erfolg unseres Programms. Extern zusammengesetzte Rezepturen sind für unsere Arbeit in der Regel nicht praktikabel und gefährden den geschützten Charakter unserer Lösungen“, so Darrin Teeter. Die Möglichkeit, auch technische thermoplastische Formteile und thermoplastische Verbundwerkstoffe herzustellen, eröffnen für das Unternehmen zudem eine völlig neue Dimension der Vielseitigkeit und Wertschöpfung.
Enge Zusammenarbeit mit führendem Forschungsinstitut NIAR
Wichtiger Partner in diesem Projekt ist das NIAR Institut ATLAS (Advanced Technologies Lab for Aerospace Systems) in Wichita, Kansas. Mit 1400 Mitarbeitern und einem jährlichen Forschungsbudget von mehr als 240 Mio. USD ist NIAR (National Institute for Aviation Research) die führende Forschungseinrichtung auf dem Gebiet der Luftfahrt in den USA. Seit Mitte 2023 betreibt ATLAS eine GX 450-1400 in seinem 150.000 qm großen Forschungstechnikum, die unter anderem auch für das FiberForm und ColorForm-Verfahren ausgelegt ist. Darrin Teeter: „Als wir das Potenzial entdeckten, unsere LCTS-Materialien im thermoplastischen Spritzguss herzustellen, konnten wir die Labormaschine bei ATLAS nutzen, um wichtige Prozessvalidierungsprozesse durchzuführen. Die Ergebnisse waren hervorragend, so dass wir uns schnell für den Kauf der DCIM-Anlage entschieden haben.“
Die GX 1100-4300 DCIM Anlage mit einer Schließkraft von 11.000 KN soll im Mai ihre Produktion in Wichita aufnehmen. Hergestellt werden zunächst Werkzeugdorne für Composites-Artikel in Flugzeugen, wie Propellerblätter, Tragflächen oder Fahrwerke. Fiber Dynamics sieht für die Zukunft in der DCIM-Technologie auch großes Potenzial in der Automobil- oder Sportartikelindustrie.
Starkes Team für ein starkes Projekt (v.l.):
Brennen Shelton (General Manager, Fiber Dynamics), Eugen Schubert (Sales & Application Manager Krauss-Maffei Corporation), Darrin Teeter (CEO Fiber Dynamics), Nolan Strall (President Krauss-Maffei Corporation), Waruna Seneviratne (Director ATLAS), Christian Seyferth (Global Expert Sales KraussMaffei) und Thomas Drogi (Process Engineer) vor der GX 1100-4300 DCIM im KraussMaffei Technikum in Parsdorf
DCIM von KraussMaffei – wirtschaftlich und nachhaltig
Das DCIM-Verfahren kombiniert Spritzgießen und Compoundieren in einem Prozess. Ein Einschneckenextruder übernimmt die Materialaufbereitung, wodurch das Verfahren besonders für kleinere Bauteile mit einem Schussgewicht von 50 g bis 2000 g wirtschaftlich attraktiv ist. Materialeinsparungen von bis zu 50 Prozent pro Kilogramm können somit erzielt werden.
Der gesamte Prozess vollzieht sich in einer Wärme, denn die compoundierte Schmelze gelangt ohne Zwischenstopp oder Abkühlung in die Plastifizierung der Spritzgießmaschine. Auf diese Weise verringert sich der Polymerabbau, Energiekosten werden eingespart und der CO2-Fußabdruck reduziert.
Ansprechpartner
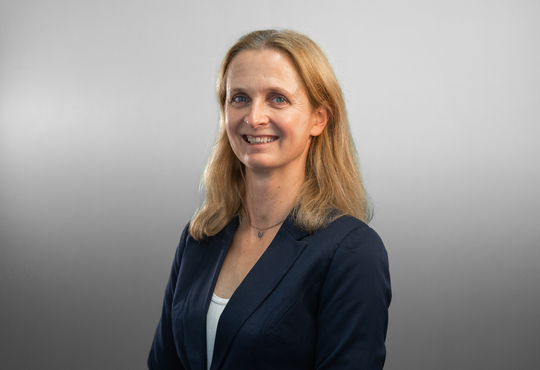
Marketing Manager Injection Molding Machinery & Contact Extrusion
Petra Rehmet
Tel +49 (0) 89 8899 2334
Email an Petra Rehmet