Das Brett mit dem Super-Pop: Kape fertigt revolutionäre Skateboards mit Equipment von KraussMaffei
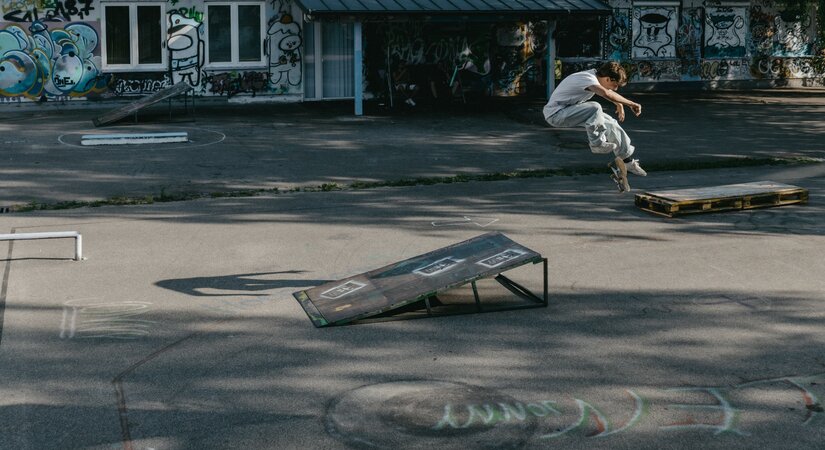
- Wesentlich langlebiger als schichtverleimte Holz-Bretter
- Glasfaser Sandwich Composite mit Schaumkern
- In-Situ-Polymerisation mit Caprolactam aus rezyklierten Fischernetzen
(Parsdorf, 16.09.2024) Probieren, hinfallen, aufstehen, weitermachen. Sowohl als Skateboarder als auch als Unternehmer braucht man Wagemut und Ausdauer um erfolgreich zu sein. Peter Karacsonyi hat und ist beides. Nach mehr als zehn Jahren Entwicklungszeit hat er mit Hilfe von KraussMaffei nun das perfekte Skateboard geschaffen. Aus Glasfasern und recyceltem Polyamid – und eben deshalb viel nachhaltiger als bisherige Holzmodelle.
Jeden zweiten Tag ein neues Brett: Profi-Skateboarder, die schichtverleimte Holz-Skateboards fahren, müssen diese extrem häufig wechseln, denn die „Decks“ genannten Bretter splittern leicht und verlieren durch Mikrorisse ihre Spannung. Dann braucht es immer mehr Energie, um bei Tricks spektakulär hoch abzuheben. Das Brett verliert seinen „Pop“, wie es in der Fachsprache heißt. Für Peter Karacsonyi, seit der Kindheit begeisterter Skater und Skateboardbauer, war klar, dass sich etwas ändern muss. Mehr Pop, bessere Performance, mehr Nachhaltigkeit und einfachere Fertigungsprozesse lauteten seine Ziele. Nach zehn Jahren Entwicklung mit Probieren, Hinfallen, Richtungswechseln und hartnäckigem Weitermachen ist er nun am Ziel: Das Deck „Vanguard“, hergestellt mit Fertigungsequipment von KraussMaffei, ist ein ausgefeiltes Composite-Bauteil, bestehend aus Glasfasern und Polyamid. Ende August kam die erste Kleinserie auf www.kapeskateboards.com auf den Markt und war innerhalb von fünf Stunden ausverkauft.
Weltweiter Millionenmarkt
Weltweit werden pro Jahr etwa fünf bis sieben Millionen Skateboards verkauft. Wer die Fertigung des Sportgeräts verändern will, muss also die industrielle Großserienproduktion im Auge behalten. Ein starker Konzern im Rücken ist da hilfreich – aber für die Revolution selbst braucht es ein kleines und schlagkräftiges Team. Die Spezialisten des KraussMaffei Standorts Georgsmarienhütte/Harderberg – vor allem Konstrukteur Florian Jovanovic und Werksleiter René Ring – waren genau die Richtigen. Peter Karacsonyi lobt:
Der Formenträger, der gemeinsam entstand, ist extrem flexibel mit vielen Einstellmöglichkeiten – und dennoch so einfach und günstig wie es eben sein muss, wenn jemand am Beginn seines Projektes steht. Wobei die Zusammenarbeit mit KraussMaffei eigentlich der erfolgreiche Schlussspurt war.
Seit 2014 hatte Peter Karacsonyi getüftelt. Zunächst mit einem verpressten Mehrschichtsystem aus Holzfurnieren und Carbonfasern. Mit der Idee konnte er in der Fernsehshow „Höhle der Löwen“ zwei Investoren überzeugen und verkaufte mehrere Tausend Bretter. Sogar ein Weltrekord wurde mit diesem Board aufgestellt. (Hier der Link dazu: https://www.youtube.com/watch?v=iGV6ZNn2y_k )
Das war Peter Karacsonyi jedoch nicht genug. Denn als sich mit der Technologie keine Verbesserung mehr erreichen ließ, entstand die Idee, Skateboards zu gießen anstatt sie zu pressen, Organosheets aus Glasfasern zu verwenden und im Spritzguss mit einer Rippenstruktur zu versehen. Schon hier war klar, dass der verwendete Kunststoff ein Thermoplast sein sollte, weil dabei die Recyclingmöglichkeiten wesentlich besser sind. Das Konzept wurde ausgearbeitet und patentiert, aber letztlich nicht umgesetzt, weil aufgrund der hohen Wandstärke und der Komplexität des Prozesses die Zykluszeiten zu hoch gewesen wären.
In-situ-Polymerisation als Lösung
Also erneut umgedacht. Durch sein Studium der Sportgerätetechnik ist Peter Karacsonyi mit Fertigungsprozessen vertraut – und er ist ein sehr gründlicher Mensch. Deshalb nahm er als nächstes die In-Situ-Polymerisation in den Blick. Dabei wird der Kunststoff nicht in Granulatform verarbeitet, sondern seine Grundstoffe reagieren erst im Werkzeug selbst miteinander. Für das Polyamid ist das Caprolactam plus Aktivator und Katalysator. Caprolactam ist flüssig wie Wasser. Das Verfahren versprach deshalb eine besonders gute Durchdringung der Glasfasern. Zudem würde es im Gegensatz zum Spritzguss ermöglichen, in einem One-Shot-Prozess ein Sandwich-Composite herzustellen. Hierbei sollte ein selbst entwickelter Schaumkörper (ebenfalls aus Polyamid) als leichtes Kernmaterial dienen. Nachdem ein händischer Versuch gezeigt hatte, dass sein Konzept funktioniert, machte sich Peter Karacsonyi auf die Suche nach Industriepartnern für die Herstellung des Decks – sie endete frustrierend. Denn Anbieter in Österreich und Ungarn lieferten nicht die gewünschte Qualität und die Zusammenarbeit erwies sich als wenig partnerschaftlich.
Mit eigener Fertigung alles auf eine Karte gesetzt
Wer am hohen Rand einer Halfpipe einen Handstand machen will, muss alles auf eine Karte setzen. Auch Peter Karacsonyi ging deshalb „all-in“ und beschloss, die Fertigung des Vanguard in die eigene Hand zu nehmen. Das hieß: Suche nach einer entsprechenden Produktionsanlage, bestehend aus Formenträger, Werkzeug, Dosiermaschine und Automatisierung. Um seine Vision auch finanziell umsetzen zu können, akquirierte er Forschungsgelder und holte Investoren ins Boot. Seit 2019 galt der ausschließliche Fokus dem Composite-Deck, die Fertigung der früheren Boards wurde eingestellt.
Mit dem Team von KraussMaffei in Georgsmarienhütte/Harderberg stimmte von Anfang an die Chemie und so konnte man gemeinsam Herausforderungen bewältigen. Neben der mechanischen Flexibilität – aus prozessspezifischen Gründen sollte der Formenträger möglichst beweglich sein – war es vor allem die ungewohnt hohe Werkzeugtemperatur, die Kopfzerbrechen bereitete. Normalerweise herrschen hier 40 bis 60 Grad Celsius, für das Skateboard brauchte es aber 140 bis 160 Grad. Viele Standardkomponenten wie Zylinder und Ventile ließen sich deshalb nicht verwenden und mussten durch Alternativen ersetzt werden. Um den Energieverbrauch möglichst niedrig zu halten und nicht die gesamte Metallkonstruktion aufzuheizen, wurden Werkzeug und Formenträger mittels Isolierplatten thermisch voneinander getrennt. Durch den Einsatz eines Luftkissens lassen sich Ober- und Unterteil kraftvoll zueinander verschließen. „Das Ganze ist fast organisch gewachsen“, erinnert sich Konstrukteur Florian Jovanovic an die gewonnenen Erkenntnisse während der Entwicklung. Das Ergebnis ist ein verlässlicher Serienprozess mit optimal abgestimmter Anlage.
Sandwich aus Glasfasern und Schaumkern
Für jedes Board nimmt der Kape-Mitarbeiter nun ein Sandwich aus unidirektionalen Endlos-Glasfasern und zwischenliegendem Schaumkern und legt es in das Werkzeug ein. Der Formenträger schließt, das Vakuum wird angelegt und die Polyamidkomponenten hinzu dosiert. Auch beim Caprolactam hat es sich Peter Karacsonyi übrigens nicht einfach gemacht. Um – über die verlängerte Lebensdauer hinaus – noch mehr Nachhaltigkeit in sein Brett zu bringen, fand er in Italien einen Anbieter für das Monomer, der es per chemischem Recycling aus Fischernetzen und Industrieabfällen gewinnt. „Die Zusammenarbeit mit Peter bei diesem Projekt war großartig! Die Herstellung des Skateboards mit ECONYL® Caprolactam war eine einzigartige Erfahrung. Und was es noch besser machte, war die Tatsache, dass wir dieselben nachhaltigen Werte mit dem Team teilten - das hat den Unterschied ausgemacht.“ , so Giulio Bonazzi - Vorsitzender und CEO von Aquafil SpA.
Nach rund sechs Minuten öffnet das Werkzeug und das 80 mal 21 Zentimeter große Vanguard kann entnommen werden. Als Nacharbeit ist nur das Entfernen eines hauchzarten Polyamid-Randes und des 0,7 Millimeter dicken Angusses nötig, was einfach mit einem Messer geschieht. Die sichtbare Struktur des Decks prägt die Optik, nur Klarlack und ein Siebdruck werden noch aufgebracht.
Der Käufer des Vanguard muss nur noch seine Achsen anschrauben, dann kann es losgehen. Ohne Splittern oder Brechen – aber mit Pop, der bleibt und dem Gefühl und Klang von Holz. Das bestätigen auch die bisherigen Testfahrer, zu denen unter anderem mehrere Olympiateilnehmer und Kape-Teamrider Levi Löffelberger zählten. Seit den 1970er Jahren war die Fertigung von Skatebaords mehr oder minder gleich geblieben. Die innovative Composite-Technologie von Peter Karacsonyi / Kape mit dem Equipment von KraussMaffei ändert das jetzt.
Messebesucher der Fakuma können das Vanguard live auf dem KraussMaffei-Stand erleben (15. – 19. Oktober, Halle A7, Stand 7303).
Ansprechpartner
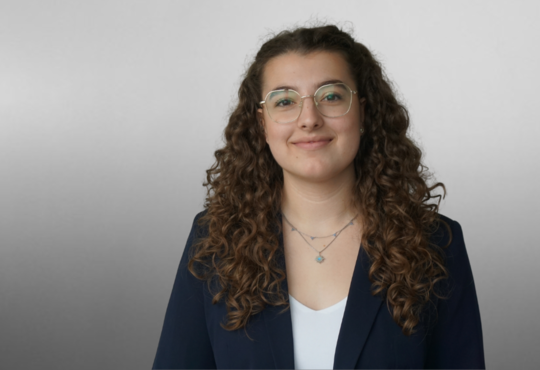
Marketing Manager Reaction Process Machinery
Rebecca Böhm
Tel +49 89 8899 3656
Email an Rebecca Böhm