Cityflieger im Aufwind – mit FiberForm-Technologie von KraussMaffei
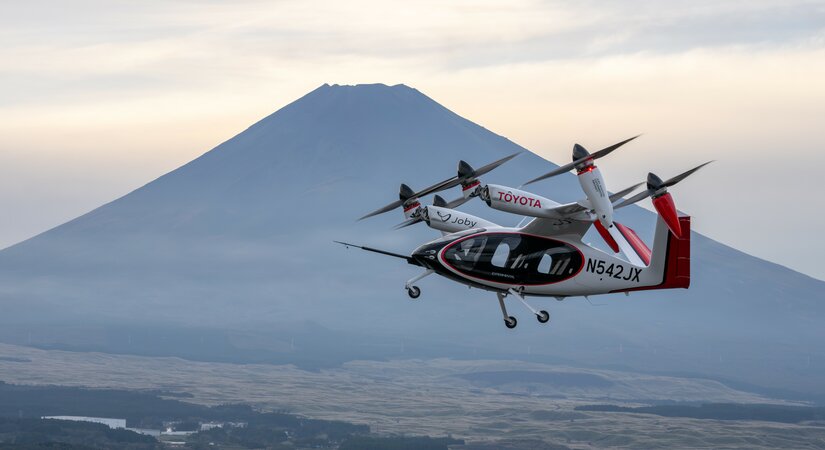
- Renommiertes NIAR-Institut setzt auf thermoplastisches Composites-Verfahren für hochkomplexe Rippenstrukturen
- 3000-mal schnellere Fertigung im Vergleich zu Metall
- Mehr Designfreiheit und bessere Kosteneffizienz
Parsdorf/Wichita, USA (09.04.2025) KraussMaffei und das National Institute for Aviation Research (NIAR) der Wichita State University, USA, setzen neue Maßstäbe im thermoplastischen Leichtbau für die Luftfahrt. Gemeinsam haben sie ein innovatives Strukturbauteil mit komplexer Rippenstruktur entwickelt, das speziell für eVTOL-Luftfahrzeuge konzipiert wurde – elektrisch betriebene Fluggeräte, die senkrecht starten und landen können. Zum Einsatz kommt das bewährte FiberForm-Verfahren von KraussMaffei. Das Ergebnis: Die Fertigungszeit reduziert sich von über 100 Stunden auf nur zwei Minuten im Vergleich zur Metallvariante – bei gleichbleibender Festigkeit und Sicherheit.
Beim FiberForm-Verfahren wird ein sogenanntes Organoblech, thermoplastisch imprägnierte Endlosfasern, ins Werkzeug eingelegt, geformt und umspritzt. Im Vergleich zur Fertigung von Bauteilen aus Metall bietet diese vollautomatisierte Kombination aus Thermoformen und thermoplastischem Umspritzen deutliche Vorteile wie geringere Kosten, weniger Eigengewicht und ein Bruchteil des zeitlichen Aufwands. Und das bei gleicher mechanischer Festigkeit und Sicherheit. Gleichzeitig erlaubt das FiberForm-Verfahren deutlich mehr Designfreiheit.
Beim NIAR „Advanced Technologies Lab for Aerospace Systems“ (ATLAS) geschieht dies auf einer GXW 450-2000/1400 von KraussMaffei mit einer Schließkraft von 4500 kN und einer Wendeeinheit sowie einer passenden Automationslösung mit zwei IR-Industrierobotern.
Treiben gemeinsam die Entwicklung des thermoplastischen Leichtbaus in der Luftfahrt voran: Induwara Herath (Research Engineer, NIAR ATLAS, Eugen Schubert (Sales and Applications Manager, IMM & Automation bei KraussMaffei) und Dr. Waruna Seneviratne (Leiter NIAR ATLAS) vor der GXW 450 FiberForm im NIAR ATLAS Labor (v.l.)
3000-mal schnellere Fertigung als mit Metall
Die kurzen Taktzeiten im Vergleich zu Metall werden besonders deutlich bei der neu entwickelten und erprobten Rippenstruktur. Traditionell werden Bauteile dieser Art aus einem massiven Metallblock gefräst – ein Verfahren, das mehr als 80 Prozent des Materials entfernt und über 100 Arbeitsstunden in Anspruch nimmt. „Im Gegensatz dazu wurde das thermoplastische Bauteil aus einem flachen Organoblech in weniger als zwei Minuten geformt und umspritzt. Die ausgewiesene Expertise der beteiligten Partner war entscheidend für diesen Erfolg“, erklärt Dr. Waruna Seneviratne, Direktor von NIAR ATLAS. Neben KraussMaffei waren die Firmen Joby Aviation, Toyota, Victrex und Prospect an der Entwicklung beteiligt. Das Projekt ist Teil des “Manufacturing for Affordable Sustainable Composites” Programms des Air Force Research Laboratory.
Von der automobilen Großserie profitieren
„Die Ergebnisse unterstreichen das Potenzial der aus der Automobilindustrie bekannten FiberForm-Technologie für die Serienfertigung von Primär- und Sekundärstrukturen in der Luftfahrt“, so Seneviratne weiter. Eugen Schubert, Sales and Applications Manager, IMM & Automation bei KraussMaffei, betont die Bedeutung des NIAR ATLAS-Labors als Innovationsplattform: „Das NIAR ATLAS Institut bietet eine ideale Umgebung, in der Maschinenhersteller, Materiallieferanten und Werkzeugentwickler gemeinsam mit Flugzeugherstellern neue Materialien und Prozesse risikofrei für anspruchsvolle Luftfahrtanwendungen erproben und für die Serienreife entwickeln können.“
Fortführung des Erfolgsprodukts „Prachter“
NIAR ATLAS und KraussMaffei arbeiteten bereits 2024 erfolgreich zusammen. Damals ging es um im FiberForm-Verfahren hergestellte Fensterverschlüsse, die für die Umrüstung von Passagier- zu Frachtflugzeugen, sogenannte Prachter, zum Einsatz kamen. Die Fensterverschlüsse wurden in nur 90 Sekunden produziert und waren 20 bis 30 Prozent leichter sowie nur halb so teuer wie ihre Pendants aus Metall.
Mit der neuen, komplexen Rippenstruktur demonstrieren die Entwicklungspartner die FiberForm-Technologie nun an einem anspruchsvollen Strukturbauteil und ebnen den Weg für weitere Anwendungen sowie die erfolgreiche Zertifizierung in der Luftfahrt.
Ansprechpartner
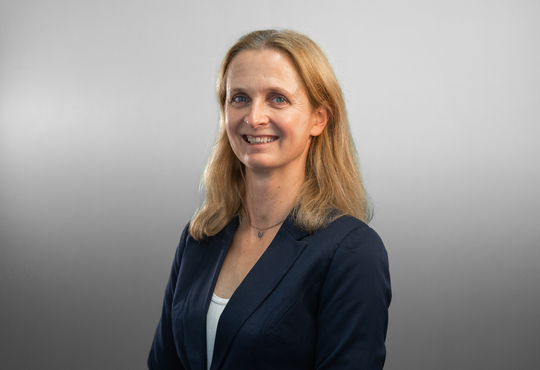
Marketing Manager Injection Molding Machinery & Contact Extrusion
Petra Rehmet
Tel +49 (0) 89 8899 2334
Email an Petra Rehmet