Aus dem Meer in den Tunnel: KraussMaffei Kunde Oldroyd nutzt 100 Prozent Seaplastics für seine Produkte
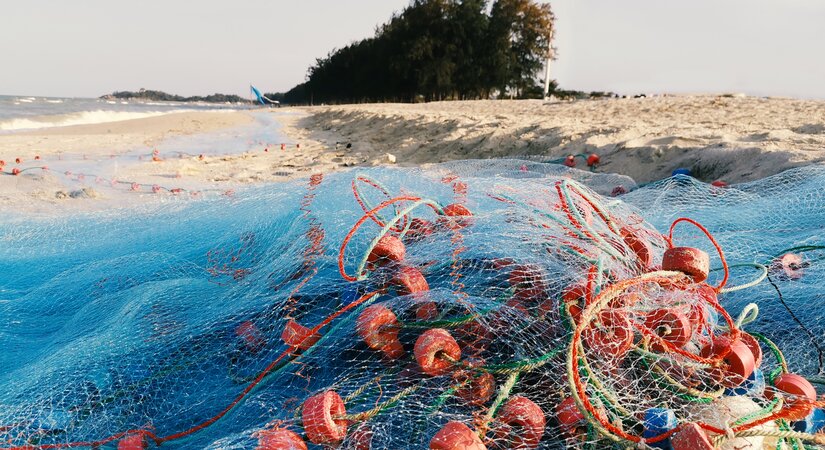
- Drei CX 160-750 mit LRX-Robotern in Übergröße
- In Kürze: weitere CX 160 mit 2K-Ausstattung
- Durch mannlose Wochenendschichten konkurrenzfähig
(München, 30.01.2023). Was haben ein Tunnel und ein Wanderschuh gemeinsam? Beide verfügen über eine Membran gegen Regennässe. Im Fall des Tunnels ist die Norwegische Firma Oldroyd Spezialist für die Membran und ihre spritzgegossenen Befestigungsartikel. Dafür verwendet sie CX-Maschinen von KraussMaffei und zu 100 Prozent Seaplastics.
In Skandinavien gehören Tunnel zum Alltag – man nutzt sie um die vielen Fjorde zu umgehen. Allein Norwegen verfügt über 900 Stück davon, und auch der weltweit längste Straßentunnel steht hier. Die Einhausungen für den Verkehr sind komplexer als man meint, denn hinter der für den Fahrer sichtbaren Röhre verbirgt sich ein anspruchsvolles Membransystem. Es verhindert, dass durchs Erdreich eindringendes Wasser Schäden am Beton verursacht.
Oldroyd ist der Platzhirsch im Bereich Regenabdichtung und verfügt über rund 90 Prozent Marktanteil in den nordischen Ländern. Der Schlüssel für den Erfolg liegt in der Innovationskraft des Familienbetriebes in Stathelle (rund 160 Kilometer südwestlich von Oslo). Ursprünglich in der Folienextrusion beheimatet, hat sich Gründer John Oldroyd Cheetham mit Hilfe von KraussMaffei auch die Technologie des Spritzgießens erschlossen und betreibt jetzt erfolgreich drei hydraulische CX 160-750 mit einer Schließkraft von 1600 kN.
Darauf entstehen in etwa 15 Sekunden Zykluszeit sogenannte Spacer, gewölbte Artikel mit Gitterstruktur, die einen Abstand zwischen Gestein und Membran schaffen. Das Gewicht liegt bei etwa 150 Gramm, wobei es um die 20 verschiedene Modelle gibt, deren Durchmesser und Höhe variieren.
100 Prozent Seaplastics
Für einen Tunnel allein werden 300.000 bis 400.000 der Spacer benötigt. Bei diesen Mengen zahlt es sich ökologisch besonders aus Recyclingmaterial einzusetzen. Oldroyd verwendet zu 100 Prozent „Seaplastics“, das etwa hälftig aus PP und PE besteht. Die Überbleibsel von kaputten Fischernetzen und Kunststofftauen werden an Norwegens Küste von darauf spezialisierten Firmen gesammelt, zerkleinert, gewaschen und regranuliert. Der dezente Fischduft muss für den Tunnelbau nicht extra entfernt werden.
Bei den wechselnden Materialzusammensetzungen und daraus folgenden Viskositätsschwankungen ist die Maschinenfunktion APCplus hilfreich. Sie sorgt für ein sehr konstantes Schussgewicht, indem sie den Umschaltpunkt und die Nachdruckhöhe von Schuss zu Schuss anpasst.
Sichere Geisterschichten am Wochenende
Um in Europa Kunststoffartikel wettbewerbsfähig produzieren zu können, benötigt man eine leistungsfähige Automation. Alle Oldroyd-Maschinen sind deshalb mit LRX-Robotern von KraussMaffei in Übergröße ausgerüstet. Durch ihre sehr lange vertikale Achse können diese große Mengen von gefertigten Artikeln aufstapeln – beginnend bei einer ebenerdigen Palette bis in eine Höhe von zwei Metern. Bei den Tunnel-Spacern umfasst dieses Volumen genau die Produktion eines (mannlos gefahrenen) Wochenendes.
2K-Projekt mit TPE
Bald wird bei Oldroyd eine neue CX mit Zweikomponenten-Ausstattung in Betrieb gehen, denn John Cheetham hat erneut eine Entwicklung gemacht, die den Tunnelbau verändern wird: eine 2K-Platte, genannt RoadStar, die auf den Stahlstäben fixiert wird, welche die Betonwandung mit der Gesteinsschicht verbinden. Bislang bestehen diese Platten aus Metall und korrodieren entsprechend, weshalb es Wartung und nach etwa 50 Jahren einen Austausch braucht. Die Roadstars hingegen wurden in speziellen Alterungstests auf eine Lebensdauer von 120 Jahren veranschlagt. Allein dies spart eine Menge Ressourcen. Der RoadStar wurde von Oldroyd-Kunden bereits getestet und stieß auch deshalb auf Zustimmung, weil die integrierte TPE-Schicht abdichtend wirkt, während die andere Seite (aus PE) schlagfest ist. Bei einem Markterfolg und den entsprechend hohen Stückzahlen werden weitere 2K-Maschinen den Weg von München nach Norden antreten.
Ansprechpartner
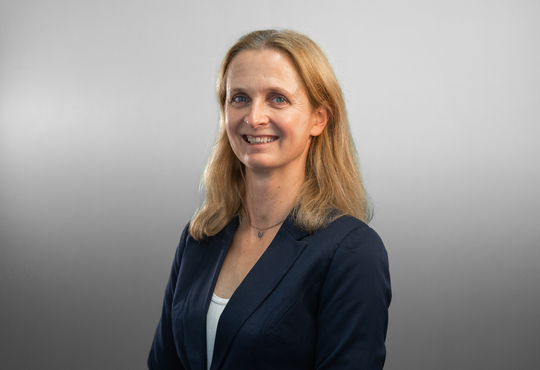
Marketing Manager Injection Molding Machinery & Contact Extrusion
Petra Rehmet
Tel +49 (0) 89 8899 2334
Email an Petra Rehmet